COMPOSITES
We are driven by the need to explore and create. As part of that commitment, we draw on synergies and transfers of knowledge from other industry sectors.
We have developed previously unimagined applications for fibre composite technology; we push boundaries in our development of workable solutions whose key goal is even greater reliability
Lightweight construction
There is only one route to saving weight and keeping costs in check: fibre composite technology.
Fibre composite materials are pre-destined for lightweight construction as the material can easily be tailored to match bespoke structural demands.
Large-scale, complex parts clearly offer the greatest potential for weight savings compared to metal, and that is precisely where we excel.
We integrate pre-manufactured fittings into composite structures that deliver effective fire protection and use laser technology and 3D tracking systems for perfect alignment and orientation.
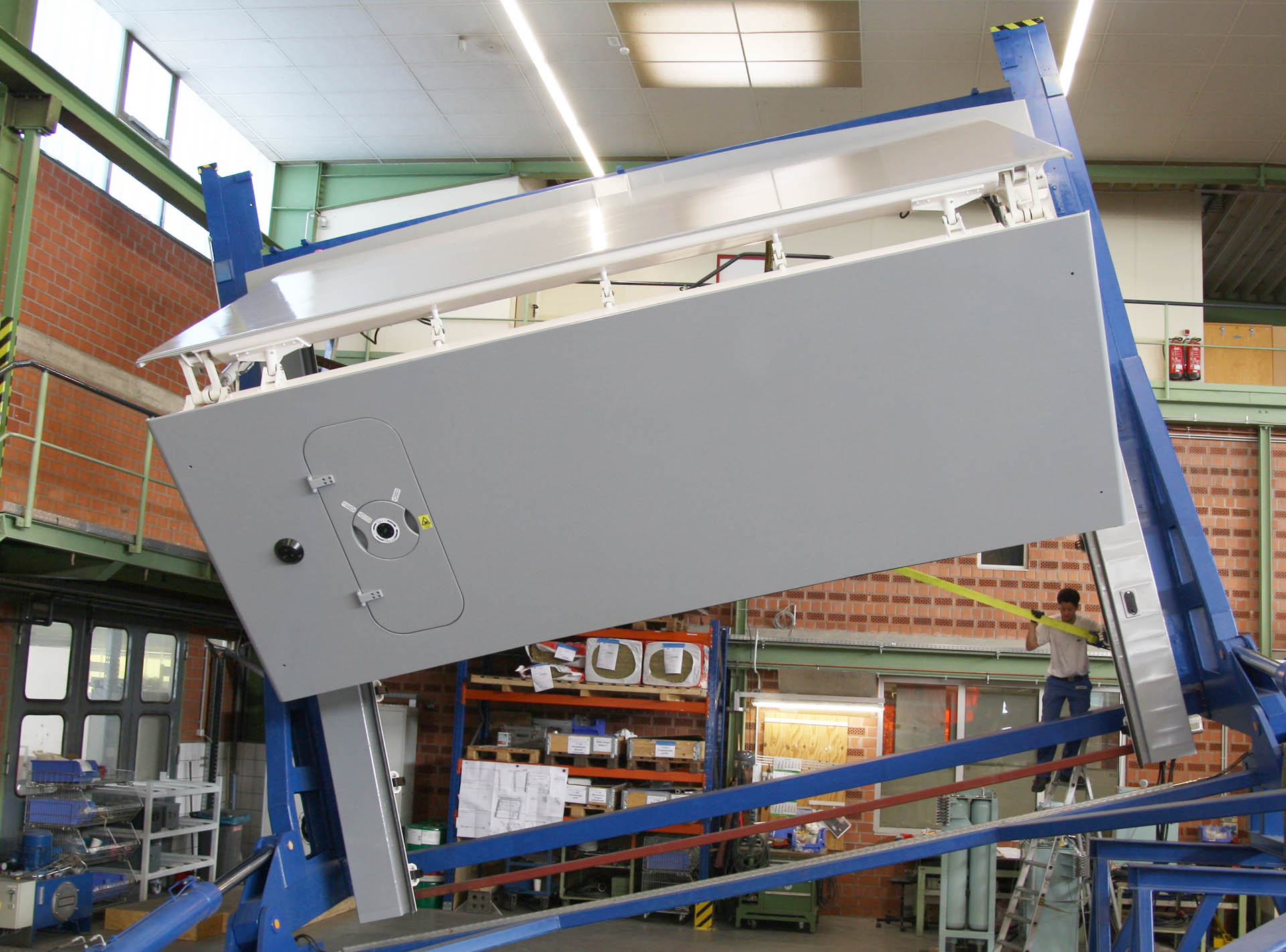
Proteccore (Ballistic) and Fire resistance Tests
Proteccore® technology for bulletproof fibre composite panels. For:
- great flexural stiffness.
- low weight, up to 60% weight reduction compared to steel plates.
- protection is provided on both sides.
- excellent heat insulation.
You can add effective security with our Proteccore® ballistic protection system and remain virtually invisible with a low radar signature and our CRP-based electromagnetic shielding system.
We have a certificate for flame retardancy according to the IMO.
FIBRETEMP®
Award-winning patented technology.
We integrate carbon resistance heating technology into the mould structure for maximum dimensional stability:
- no heat distortion
- no warping
- ultra-light weight thanks to carbon fibre reinforced polymer (CFRP) sandwich construction
- super-fast cycle times as a result of heating precise areas of material.
Our solution uses 90% less energy than external heating
RENEWABLE MATERIALS RESEARCH
Building with flax-fibre sandwich panels, the renewable alternative:
- Near identical mechanical properties to conventional composite panels
- Only slightly heavier
- Better fire resistance / retardance
- Flax fibres are hollow, giving more stability on impact
- Cork core has better acoustic properties than conventional panels
- Ultimate sustainability – cork regrows without harming the tree